Top Reasons Why You Should Utilize Zinc For Die Casting
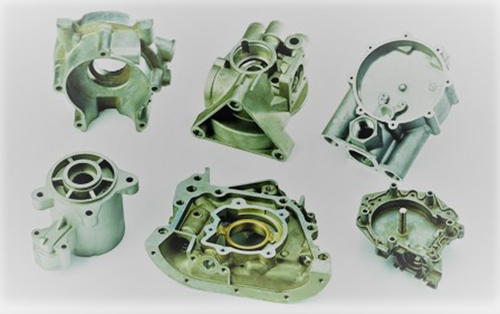
Zinc
is often ignored by many engineers while choosing material for
designing components through the die casting process because when it
is about weight, zinc is heavier than aluminum and magnesium. In
short, weight is the main reason why many manufacturers often ignore
zinc, but the fact is that it is the only remarkable drawback of
zinc. Coming to the point, if you compare the pros and cons of ChinaZinc Die Casting, you will find
that it provides more benefits than other materials.
You
may continue reading this article to explore the main advantages of
China Zinc Die Casting
and how it can be beneficial for you.
- Not the Heaviest: True that zinc is heavier than both aluminum and magnesium, but compared to other materials that can be used in die casting, zinc is a lightweight material. So, the weight shouldn't be a matter of concern for you when choosing China Zinc Die Casting for the production because it provides several other advantages as well.
- Superior Castability: One of the most significant advantages of zinc is that is the most fluid alloy, which is the main reason why many engineers now prefer it over other alloys. In simple words, zinc possesses great fluidity, which means die castings can be made thinner and it also becomes possible to put complex designs on them and that too without secondary operations. On the other hand, when using aluminum or magnesium alloys, you need to spend a decent amount of money on secondary operations for surface finishing, which eventually increases the overall production cost, but it isn't the case with zinc die casting.
- Low Tooling Cost: Investing in quality tooling is the major upfront cost in die casting and the tools used in the production are basically of heat-treated steel, which is why overall tooling cost in zinc die casting is very low because of the low melting point of zinc. It is believed that the dies used for zinc parts may last up to 10 times and 5 times longer than the dies used for aluminum and magnesium respectively.
- Faster Cycle and Stronger End Products: Zinc has the ability to be cooled at a faster rate than aluminum and magnesium, which is why it provides a better production rate and what's more, zinc alloys are stronger at room temperature than other alloys.
Conclusion:
Production can be done at a faster speed without investing a large
amount in tooling costs and the final parts are strong as well as not
so heavy.
Comments
Post a Comment