Why Should You Choose Zinc for Die Casting?
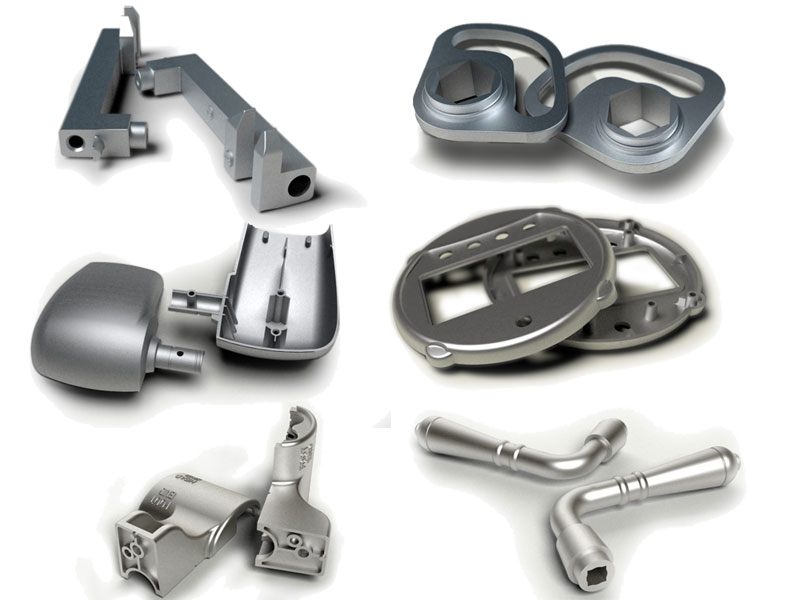
The die
casting is a manufacturing process in which the molten metal is used to
form a mold cavity under high pressure. Nowadays, several options are
available so that the manufacturer can pick the most appropriate metal
for the mold cavity. You can choose from zinc, copper, magnesium,
aluminium, lead, and pewter, but if you want to earn a good profit while
delivering a high-quality product, then you should opt for the Zinc Die Casting.
Yes, there are many benefits of using zinc as molten metal in the die
casting process and some of them are mentioned in the following blog.
Excellent Fluidity: Comparing to the aluminium, zinc has a better ability to be cast thinner and more accurately. Thus, if you are manufacturing something that should have intricate details, then you should use zinc as molten metal.
Better and Swifter Cycle Times: If you are using hot chamber die casting with zinc as molten metal, then you already know that it gives faster cycle times as the user doesn’t need to pour the molten metal into the gooseneck. It provides the opportunity to earn more profit.
It Reduces the Power Consumption: As the zinc melts at a much lower temperature compared to aluminium, thus, less power is used in the Zinc Die Casting process. Zinc melts at 800° Fahrenheit, whereas aluminium melts 1200° Fahrenheit and you know that you can save a good amount of your money by reducing the power consumption in melting and heating process.
Quality of the Product: The weight of the zinc can be a big disadvantage in the manufacturing of various applications, but for many products, it is beneficial. For example, if you want to build something which should be thin, then Zinc Die Casting will be best.
For more information visit us at http://www.china-casting.biz/die-casting.html
Comments
Post a Comment